About Us
The flexible partner for you.
AS Valdek is a family-owned business that has been providing high-quality sheet metal products and services for over 30 years.
At Valdek, we pride ourselves on being a sheet metal fabrication company that values flexibility at every level of our operations. We believe that by embracing flexibility in our processes and thinking, we can deliver transparent, effective results that not only meet your needs but also contribute to reducing our environmental footprint.
AS VALDEK was founded by Mihkel Valdek in the early years of Estonia’s regained independence. As many companies back then, we also started in a garage.
Over the years, we have preserved our status as a family business, even as we’ve grown into a larger company with a team of 80, including 8 family members.
At the end of 2023, we moved to a new stage with the completion of our newly built factory, marking a significant milestone for the company.
This transition also marked the passing of the torch, as three of the founder’s sons took over the leadership, bringing fresh perspectives while staying true to the company’s roots.

“I told you so!”
Our founder Mihkel Valdek’s favourite phrase, which is often heard around in the company. While it is said as a playful joke, we believe the statement to be true. His motivation, knowledge and intuition is the success to the growing company.
1991-1999
2000-2008
2009-2016
2017-2024
We-Solutions

We are part of tomorrow.
Flexible Work Hours and Vacations
We understand the importance of work-life balance and offer flexible work hours to accommodate our employees’ diverse needs. Whether it’s adjusting start and end times or working remotely, we provide the flexibility needed to balance personal and professional responsibilities. Our vacation policy ensures employees have the time to recharge, leading to a happier, more productive workforce.
Opportunities for Growth and Flexibility
We offer opportunities for employee growth and advancement, with roles that adapt to evolving skills and interests. This flexibility allows us to support flexible work arrangements and vacation schedules, making it easier to relocate employees when needed.
Team Building Activities
We organise events that enhance communication, build trust, and boost morale, creating a positive and productive work environment. Key events include:
Monthly Birthday Lunch Party: Celebrating each month’s birthdays with a lunch gathering.
Christmas Dinner Party: A festive dinner with the whole team.
Children’s Christmas Party: A special celebration at a children’s theatre, including gifts from Santa for the kids.
Summer Holiday: A 2-night stay with family at a seaside resort, featuring teamwork activities such as sports, dance competitions, yoga, sauna, and children’s events like arts and crafts, games, and treasure hunts.
Tallinn Autumn Run: Around 30 of our team members take part in the run, proudly wearing company shirts, with all entry fees covered by the company.
Health and Wellness Programs
We offer compensation that can be used for health services, sports opportunities, rest, and health insurance. We also use apps to encourage physical activity outside of work, organising various sport competitions that are inclusive for all fitness levels
Support for Life’s Milestones
We support our employees during significant life events, such as anniversaries, births, and marriages, reinforcing our commitment to their well-being and happiness.
Community Engagement
We invest in our community by supporting local sports teams, including basketball and football, through charitable contributions.
A platform that connects us together.
Human Resource Management
Work Hours Tracking and Management: Automatic calculation, tracking, and prediction of work hours based on employee inputs. This includes logging entry/exit times and activity tracking, providing a streamlined time management process.
Time Off Management: Employees can easily submit requests for various types of leave, including vacation, sick leave, childcare, and more, directly through the system, simplifying time-off management.
Digital Key Access: The platform seamlessly integrates digital key access for secure entry management.
User Dashboard and Overall Management: A comprehensive dashboard provides an overview of key user-based KPIs and notifications, enhancing efficient management and decision-making.
Valdek User Portal: Work Hours Tracking and Management
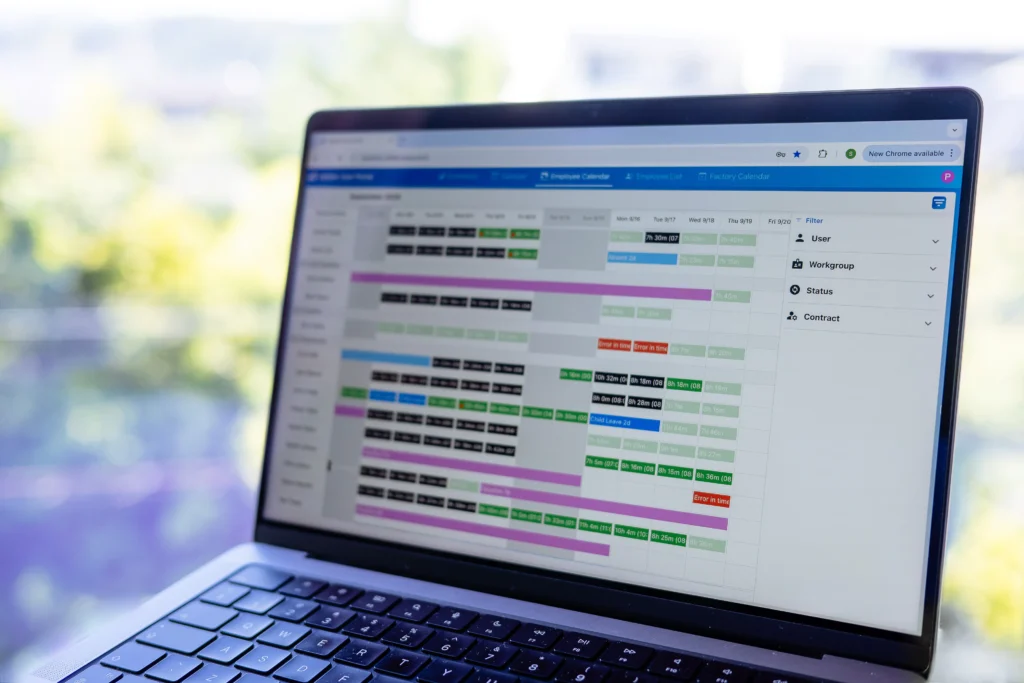
Order and Purchase Management
Email Automatic Order Entry: Clients can send new orders via email, which our system automatically processes and inserts directly into our ERP system for manual confirmation, streamlining order management.
EDI Communication: Our system supports EDI (Electronic Data Interchange), enabling efficient, paperless transactions in standardized EDI format.
Automatic PDF Order Reader: Our system includes an automatic reader that processes PDF orders and matches the articles with our database, ensuring accurate and efficient order processing.
Production and Product Management
Document Management (PDM): All related files and documents are linked and managed easily through a single interface, making document management more efficient and accessible.
Paperless Production and Digital Work Instructions: All work instructions, technical drawings, and specifications are accessible via digital devices such as tablets, eliminating the need for printed documents and ensuring a paperless production environment.
Electronic Job Tracking and Scheduling: Production schedules, work orders, and job tracking are managed entirely through software, enabling real-time updates and communication.
Full Control of Production Flow: Track and manage the entire production flow—from small components to full assemblies, covering everything from order input to delivery notes—ensuring a smooth and efficient process.
Direct Digital Link: A QR code is automatically generated for every physical part after reporting, creating a direct link between digital data and the physical product.
Digital Quality Control and Reporting: Inspections, quality checks, and reports are conducted and recorded digitally, using portable devices.
Digital Machine Logs: Equipment maintenance schedules and logs are maintained digitally, ensuring timely and accurate maintenance tracking.
Automated Data Collection: IoT devices, such as energy meters, gather data from the production floor and integrate it into management systems, eliminating the need for manual data entry.
Virtual Collaboration Tools: Digital tools facilitate design collaboration, project management, and team communication, replacing traditional paper-based meetings, notes, and drawings.
Dashboard: Manage factory KPIs through a comprehensive dashboard that provides real-time insights into production performance.
Warehouse and Delivery Management
Digital Inventory Management: Materials and products are tracked using QR codes linked to digital systems that automatically update inventory, monitor production progress, and manage logistics.
Camera Tracking Environment: Automatic stock tracking using security cameras in collaboration with Tallinn University of Technology (TalTech) and AI & Robotics Estonia.
Digital Delivery Signing/Notifications: Immediate email notifications are sent upon shipment, including digitized delivery documents, high-resolution photos, and signatures, ensuring a smooth and transparent delivery process.
Fostering a sustainable future.
Sustainable Building and Energy Efficiency
A Smartly Made Factory: Our new building reflects this commitment. It’s not just a smart factory—it’s a smartly made factory. With a production area of 6,500 m², our facility is designed for expansion, with the potential to grow up to 22,000 m². This flexibility ensures we can scale operations as needed to meet future demands, with no physical limitations on turning ideas into reality.
Eco-Friendly Roof: The roof has eco-friendly features, including an ultra-white titanium dioxide (TiO₂) coating that purifies the air by neutralizing exhaust emissions equivalent to 39 trucks. The roof’s high reflectivity doubles its lifespan compared to traditional roofing, reduces cooling costs by 50%. Additionally, the roof is partially made from recycled materials and features advanced fire protection technology.
Eco-Friendly Climate: Our facility is a passive building that requires no additional energy for underfloor heating, as it uses excess energy from our machines. With superior insulation that exceeds industry standards, we improve overall energy efficiency while maintaining stable temperatures year-round, ensuring a comfortable environment regardless of external weather conditions.
Solar Power Integration: The building is equipped with a 300 kW solar panel system installed on the roof. This system reduces our reliance on non-renewable energy sources, contributing to lower carbon emissions and supporting cleaner production processes.
Eco-Friendly Technologies
With our in-house software, we have transitioned to a paperless production system. This digital approach reduces paper waste and minimises potential mistakes, contributing to more efficient production processes and less material waste. Our digital systems also provide real-time access to information, enhancing collaboration and improving overall resource management.
Flexible and Adaptable Production
Our robotised automated process offers flexibility, allowing easy transitions to alternative machines if issues arise. This adaptability ensures we can maintain production timelines and adjust the number of machines as needed without affecting lead times. We constantly seek alternative process routes to boost efficiency and reduce costs while minimising environmental impact.
Sustainable Supplier Partnerships
We partner with suppliers who prioritize sustainability to minimize environmental impact. In our metal supply chain, leftover materials, including copper, are sent back for re-melting, and all cardboard is recycled, creating a closed-loop system that supports a sustainable supply chain.
Certificates
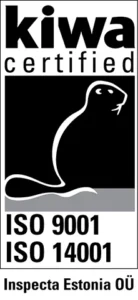
ISO 9001:2015
Quality Management System
ISO 14001:2015
Environmental Management System
AS Valdek follows these management principles:
- Reliability
- Professionalism
- High quality of products; implementation of new technologies
- High motivation of employees
- Clear and easy-to-understand rules
- Safe and healthy working environment
- Continuing development and learning by employees
- Environment-friendly production; compliance with legislation (standards and legislative acts)
- Customer requirements
In environmental management we take into account:
- Sustainable use of raw materials and recycling
- Technical condition of appliances
- Waste management
- Controlled use of chemicals
- Energy use
- Noise pollution
- Sustainable use of natural resources
We are family friendly!
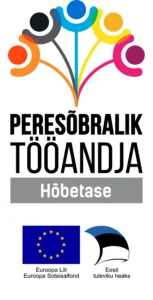
Family-Friendly Employer
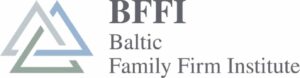
Baltic Family Firm Institute 2023

European Regional Development Fund
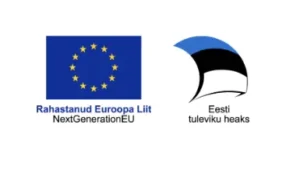
NextGenerationEU Regeneration Fund
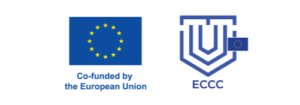
Digital Europe Programme
